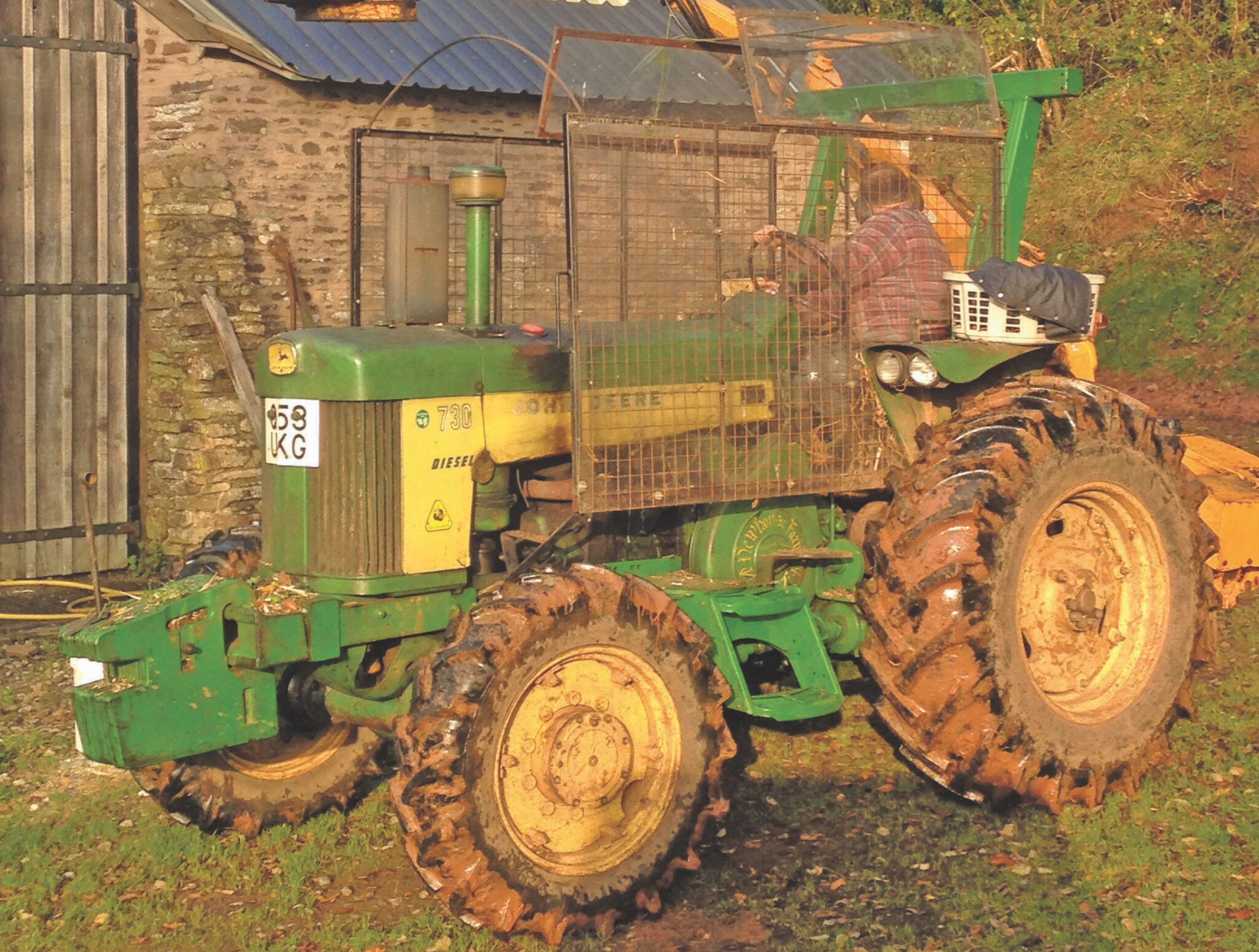
It was one of those days on vacation—glad to be away from work and I was just taking in the surroundings. Then I saw something that caught my attention and imagination. My mind kept on going back to it. It was a 730 diesel and this is where this story really starts.
In the late 1980s, I wanted another tractor. I was tired of the more usual choices with inline Perkins and Ford engines and similar. I was fed up with the treadmill of keeping them going for a few years and then having to find a replacement. I felt that I had tried the rest and now wanted the best, but I did not know what the best was. Whilst on this vacation to the first John Deere Expo in 1987, I visited the Rusty Palace and this is where I saw the 730D, a cutaway 730D. The next tractor had to be a 730D.
I grew up on a farm in Monmouthshire, South Wales, where the land is steep. A lot of it is between 1 in 4 and 1 in 3 in terms of gradient. Before my father’s time, it had been worked by horses and latterly by steam cable cultivation. My father’s first tractor was a Fordson E27N, which was followed by a succession of Fergusons. None of these tractors were four wheel drive and traction on steep ground was a challenge. We always needed more grip.
Modified Timing Case
Baling hay was the biggest challenge, as the balers were too heavy for the tractors available to us. We often used crawlers on the steepest ground, but crawlers were not so handy as a tractor. The first four-wheel drive we saw was a Fordson Major conversion supplied by Roadless Traction; we immediately realized that we had to get four-wheel drive. We bought a Roadless Fordson Super Major in 1981. Before all this, a close family friend had been one of the first, or possibly the first, in Wales to use John Deere in the 1930s. In 1968, he gave me his last John Deere when he retired. This was a 1938 “BW,” which I still own. I used it alongside the Massey Fergusons at the time and was impressed. So impressed that I arrived at my wedding on it in 1986 and took the new wife away on it. We are still married. We had heard of two cylinder John Deeres but this was one of the few that I had ever seen until we visited the first John Deere Expo in 1987.
Four -wheel drive gear
What I really wanted was a four-wheel drive 730 to replace the Ford, but no such thing was available. I realized that I would have to do my own conversion. It probably sounds like a fairly extreme solution—design and make your own. I have always been fascinated by mechanical things and engineering. This had always been a hobby and I never received any formal training in this area. I studied biology, and my Ph.D. is in alternative energies. My academic training was not connected with mechanical engineering.
New 2 and 5 selector
I was exposed to heavy engineering from childhood when I was taken on visits to the steam locomotive sheds on the railways. At the age of 12, I started to spend time at the local John Deere tractor dealers and learnt a lot of “useful expressions” as well as how to fix 4020 gearboxes, etcetera. I also learnt a lot of engineering skills when I owned a Fowler Steam Road locomotive. I did 10,000 miles on it whilst it was in my ownership and learnt to use machine tools in order to keep it at peak performance.
Transfer box
Before I could really contemplate four-wheel drive, I had to find a 730D. These were very rare in Britain and even now, there are not many around. The exchange rates after World War II meant that it was almost impossible to buy John Deere equipment in Britain. The only few that were around had come from France. After production finished in 1961, the story goes that a few more were built and dumped on the French market. I do not know if this is true, but I have seen some with serial number plates that are very different from the normal run of things. These serial number plates have a homemade look to them.
Transfer box in place
After some research, I contacted friends in the USA. A 730 stood out from the rest and seemed to have my name on it. The only problem was that it did not run too good or at all at times. I bought it and took it home, as if a souvenir, when on a business trip in 1989. After I got it back, I found that the fuel tap below the tank was turned off. I turned the fuel on and it was a different tractor. My friend said that he knew those things were good on fuel, but he had never heard of one running with the fuel turned off.
Bevel box
Once the tractor was back home, the fuel turned on and a few minor adjustments to get it running well were performed, I set about progressing the four-wheel drive project. First I needed a front axle. I had used Roadless axles on Fords for several years so I knew these well. I contacted Roadless and told them about my plan to build a four-wheel drive 730. They were very supportive and supplied a suitable secondhand axle. Several in the USA expressed an interest in this. Plans went ahead for new axles to be supplied in kits to the USA with Roadless branding. Soon after, Roadless ceased trading so the idea of supplying kits took a back seat. I have recently found that these axles are still available so the idea of supplying four-wheel drive kits is not dead.
One of the challenges when planning a four-wheel drive conversion is deciding where to take the drive from. It is important that the number of turns of the drive for every turn of the rear wheel never vary. For example, if the drive to the four-wheel drive turns 10 times (17.306 to 1 on 730) for every revolution of the rear wheels, it is important that ratio does not change or is affected by gear changes on the tractor.
Bevel box in place
The ideal is a drive point that is in constant mesh with the differential. Roadless Traction, a specialist four-wheel drive conversion, often did this by inserting a sandwich box between the final drive and gearbox, a common arrangement on Fords. Where this was not possible, such as in Nuffield tractors, they cut a hole in the side just in front of the differential. County, another four-wheel drive specialist, built many tractors based on Fords with equal size large wheels back and front. The drive was taken off the final drive pinions after the differential from each side of the tractor. There were two prop shafts to the front, one to drive each of the front wheels. When the tractor went straight ahead, all wheels went at the same speed. When the tractor turned, the wheels either side went at different speeds, but the front and back wheels at either side went at the same speed. The last new County tractor that I saw had small front wheels driven by a single prop shaft from the half shaft in the left hand rear axle. All was well when it went in a straight line. When it turned left, the prop shaft to the front slowed down; when it turned right, the prop shaft speeded up. Soon after this, County went out of business.
On a two cylinder tractor, the shafts are crosswise which, as far as that goes, makes the job easier. The shaft that you are looking for comes at least to the side of the transmission. Once you have the drive out of the tractor, the direction of rotation has to be turned through 90 degrees with bevel gears before the drive goes forward down the prop shaft to the front axle, which is something that you do not have with an inline transmission. I identified the lower shaft in the transmission as being the best option as it was in constant mesh with the differential.
The bevel box that I used was a component off the shelf. The casing on the input end was turned down in a lathe to accept a mounting, which allowed it to be bolted to a transfer box bolted to the side of the tractor. But before that, we are getting out of sequence.
The next challenge was ratios. With smaller front wheels, the aim is have the front wheels turning at between 103 percent and 107 percent of rear wheel ground speed. It might sound strange that equal speeds is not ideal. Without a third differential between the front and rear, winding up in varying conditions will be inevitable. If ratios match in a straight line, when turning a corner front and rear axles travel different distances and therefore travel at different speeds, so that wind up is a mathematical inevitability. The ideal arrangement is when in a straight line you get the feeling that the front axle is almost pulling you. To work out the ratios, account had to be taken of the reduction in the epicyclic gears in the front axle hubs, reduction in the front differential, ratios in the bevel box and the ratio between the lower transmission shaft and the back axle. Working all this out was a matter of counting up gear teeth all the way through and putting it in a spreadsheet. The other thing that we needed to know was the rolling circumferences of the front and rear wheels. I counted how many revolutions the front wheels did for 10 revolutions of the back wheels on a hard surface and on wet land. I also used published data for the rolling circumferences of the tyres on the tractor. Twenty-two teeth driving 17 teeth on the input to the bevel box gave us the ratios that we wanted.
Flywheel on
Now to explain the mechanics of how I got the drive from the tractor into the prop shaft:
I wanted to use the lower transmission shaft for mounting the gear to drive the bevel box, but its entire length was used by the sliding gear for second and fifth gears. The solution was to move the sliding gear to the top shaft so the top shaft became the sliding gear shaft. The original lower shaft sliding gear then shared the lower shaft with the new 17 tooth gear. The original top shaft was not long enough to take a sliding gear so a new and longer shaft was made and fitted so both shafts were the same length. The sliding second and fifth gear on the top shaft and selector to work that gear were also made new.
The case over the second and fifth gear area was made new from steel plate and much stronger than the original as it has to hold the bevel box, etcetera. The original cover in this area was part of the timing case cover behind the flywheel covering the timing gears and was removed. The remaining portion of the cover for the timing gears was welded up to form an independent cover for the timing gears.
The bevel box is connected to the transfer box by a spacer and flange assembly and enters the transfer box below the lower transmission shaft. The bevel box had to be mounted some distance out from the transfer box so that the propshaft would clear the flywheel guard as it passed forward. This meant that there was plenty of room for a sliding gear to select four wheel drive on the input to the bevel box.
The most important question of all is how did it turn out? Why bother—was it worth it—would I do it again? It has been a long time since the 730 arrived in 1989 and much has changed in farming. When the 730 arrived, the work was centered around livestock farming, hay, silage and moving animal feeds in winter. This has all changed—greater emphasis is placed on conservation than food production. The hay and silage machinery has been replaced by bush hogs and hedge cutters.
All this new machinery is heavier and requires more horsepower than the machinery it replaced.
As this change occurred, I questioned the wisdom of keeping the 730. There were plenty of six cylinder alternatives, but all showed signs of dying soon and I could not see why a modern tractor should be any better. The 730 stayed for a new era on the farm.
At times, buying new implements to use with a tractor that has around for half a century or more has been fun. When I bought a bush hog, the supplier asked what sort of tractor I was going to use. He had never heard of a John Deere 730 and said “Is it a four or a six, ‘cos if it is a four, it ain’t going to drive it.”
I replied, “Neither, it is a two.” He had to come and see it working before he would believe it. There is something about the torque rise of a two cylinder that makes it so effective.
It is strange these days when driving down the road, I rarely see a 20th century tractor working in our area. They have all died or have been put out to pasture. The 730 just keeps going. Tyres, clutches, brakes have all been done regularly over the years. The only failure that I have experienced came a few years ago after I had changed the hydraulic oil for the first time in my ownership. On removing the drain plug, nothing came out. The oil had been in there so long that it had to be pulled out with a screwdriver. Then a few weeks later, a fragment of metal jammed a control valve open resulting in a loss of position control. The entire assembly on the rear of the tractor had to come off. I guess that fragment of metal had been in there since the tractor was new in 1959, and if I had not changed the oil and moved that fragment, the problem would not have occurred.
Eldest daughter testing new steps
So what next? The 730 shows no signs of dying and copes with all the demands of the work and implements that are used with it. Performance over last 25 years confirms it as the best. Four-wheel drive gives that extra grip on steep land, particularly for holding back going downhill or reversing up a steep bank. Fuel economy and lugging power are outstanding. So yes—the 730 tractor is the best that I have ever used in the special conditions on a small steep farm, and if I had my time over again, I would do it again. More power would be useful. The next job is to put 830 valves in. I have a spare head that I am preparing.
By Geoff and Veronica Mathews
Monmoutshire, UK
mathews186@btinternet.com