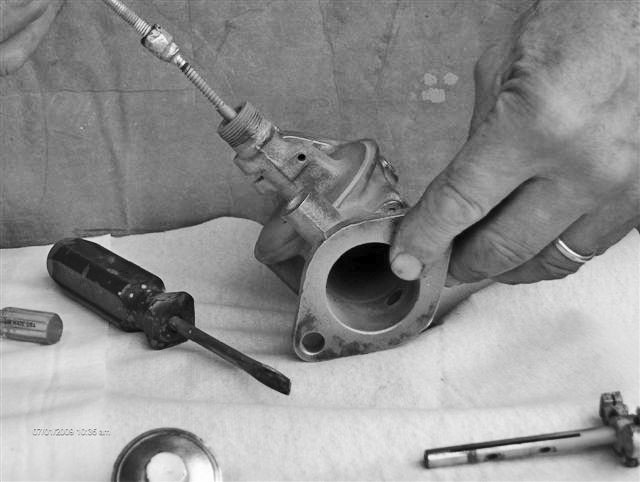
1) 420 rockshaft seal update—late breaking news
2) Strange requests in John Deere land: “Help me get this 530 running good enough to win the slow race,” carburetor tune ‘em up to slow ‘em down tips
3) The do’s and don’ts of carburetor rebuilding, JD “D” style
As we begin, happy summer to all readers. Seems as though it took this season a long time to get here and now it is going by too quickly. By the time you are reading this article, our small acreage of wheat and oats will be harvested and we will be closing in on the grand finale at our small farm—pumpkin season. We wish you could all stop by to share that time with us.
Now down to business. One thing I have learned while writing these articles for Green Magazine is that no matter what the issue, I will never know everything there is to know about all topics. As vast as the Green Magazine coverage is, and as many readers that are involved, someone out there probably knows more than I do regarding some of the topics I choose to write about each month. It never ceases to amaze me (while talking on the phone to people regarding my articles) that some callers are novices, some are lifetime hands-on experts on the subject at hand, some are very experienced retired technicians or engineers and some are “just” John Deere collectors with a passion to bring their old two cylinders to 100 percent restored, regardless of the cost or the effort needed to complete that task. Coming up with subjects to speak of is no problem for me, but trying to totally please everyone with my words on the topic is the difficult part. Still, until I hear from my boss Richard Hain (editor of this great magazine), that I should quit writing, I will continue.
So let’s all get updated, first of all, on my article from the June Green Magazine regarding the John Deere 420-430 rockshaft’s annoying oil leak problem. We spoke of original cork seals that all leaked; we spoke of an o-ring and back-up washer fix that I had come up with, and we talked about a need for a spring-loaded lip seal that would be even better IF it was available. Prior to my discussion about this topic, a short article with a picture was sent in and published in the May issue by a party that FIXED the rockshaft leak by machining o-ring grooves in the shafts and then sealing them in the bushing area. I’m sure this was a good fix, with no external cosmetic changes. I have recently been informed by two different Green Magazine readers (who took the time to give me a call) that John Deere has taken care of their leakage problems in the rockshaft area of 420s with their own JD spring-loaded lip seals. The readers both verified the small diameter seals needed as a replacement, part number AT13262T. A third caller from North Carolina stated that he had the large lip seal in his hands with a John Deere part number AM3433T.
Now, in my own case, I have moved on to other John Deere projects and have not yet purchased and used the new seals. My 420 rockshaft project is now gone home with its owner, using my o-ring fix. So my apologies to those I may have offended or misinformed by not being completely up-to-date regarding the new seals from John Deere. So, to put the zipper on this subject, all of you 420-430 rockshaft leakers out there now have three different ways to fix your leaks—one, have the shafts cut for o-rings in the bushing area; two, use the Tractor Doctor’s external o-ring back-up washer fix; or three, use John Deere’s replacement seals. I told you to stay tuned, that the ol’ Tractor Doctor would have updates and solutions as they happened regarding the leaking rockshaft.
As for strange requests from JD customers, how about this one? “Get this 530 running slow enough so that I can win the ‘slow race’ next month!” The owner of a nice 530 had recently had the cylinder head rebuilt as it should have been and was just not happy with the low-end RPMs or the way it idled. The little tractor just was not a happy idler and for the most part wanted to run fast. My advice was to give the carburetor a rebuild and clean it in the Tractor Doctor’s style and to see if that would help. Fast forward to putting the rebuilt carburetor back on the tractor and starting it up, only to be very disappointed and find that it still was not a happy slow idler.
Sometimes the best way to fix things is to use the persistence tool. First, I now needed to convince myself that the “runability” problem was the carburetor’s fault. A compression test and a quick check of the ignition circuit led me back to the carburetor. Off it came for the second time. I was fortunate enough to have a 520 nearby that did idle nicely, so off came the 520 carburetor and on to the 530 it went. The idle quality was now there, so I took the 530’s carburetor apart again. After rechecking all the circuits, I finally found the blockage. It needed to be opened up with a piece of .034 diameter wire (wire field welder wire). The wire was forced to go in and then pushed around the corner of the circuit. A reflushing with the carburetor cleaner can (with a spray tube) provided a gush of rusty matter to come out at the other end of the idle circuit; I now knew that I had found the problem. It’s too bad that I had missed it on the first go-around.
I reinstalled the carburetor and started up the 530. This time, it had excellent idle quality and both idle adjust needles affected their own cylinders that they fed with what could be a rich or a lean mixture. I now set the idle mixture on just the edge of being rich as a mixture; that is, just a tiny bit of black at the stack at its slowest idle. Idle speed was then adjusted to as slow as 300 RPM, and THEN as slow as 250 RPM, and possibly even slower for a one time setting to potentially win the upcoming slow race. The 530 came with 36 inch rear wheels, which makes their outside diameter smaller than 38s; my point here is—using smaller diameter wheels at any given engine RPM will result in slower initial tractor speeds. With the tractor in low gear and running at 250 RPMs, it was almost necessary to line it up with a fence post to see it move, so we will see how it does at the slow race. I’ll once again keep you updated.
On to our final topic for this month—the rebuilding of a JD “D” carburetor. As long as we are on the subject of proper running of the old two cylinders, let’s take the very next item that came through the shop door and go through it—a DLTX 63 from a John Deere “D.” It didn’t run well at all, high speed or low speed. So let’s go through the carburetor (again Tractor Doctor style) and see what gets done, how long it takes, what parts get installed and what sealants are used to get the rusty castings to seal again.
To get down to the root of this carburetor’s problems, one must take it apart—all apart. That means every movable and not movable part and plug until you are down to just the bare casting. So many times they come to me (with a futile attempt having been made to take them apart) with just the bowl and the fuel inlet removed and then many times after stripping off most of the screwdriver slots on all the brass plugs at the air circuit endings, they end up in front of me with a “Here, YOU fix it; I have it half apart for ya.”
My friends, the only way to bring these old rusted carburetors back to life is to first start with a 100 percent complete disassembly and that means everything. I suggest bead blasting the outer castings before heating them to remove the brass plugs. The reasoning here—to get rid of the old paint, which will allow the heat applied to the casting at the brass plug area to soak into the casting and more effectively allow for removal of the brass plugs. ALL brass plugs must be removed because these old castings have to be bead blasted to get the rust and scale out of their passages and metered ends. Carburetor cleaner or Grandma’s old secret soap will not do the job. Removal of shafts, choke and throttle is necessary (that to include the throttle shaft brass bushings, which will be worn as badly as the throttle shaft itself).
Again, I must restate—an important part to a good carburetor fix, the reason one must bead blast the carburetor is to remove all dirt, rust and old paint from inside and the outside of the casting. Once every part and plug is removed, you allow the tiny abrasive beads to get into and out of the passages to clean them and not plug them up. This also includes the removal of the carburetor’s main discharge nozzle. In this carburetor’s case, the discharge nozzle was rusted into the casting and it would not fall or pull out. One must not get too western (rough) with this delicate piece, as it is made of brass and full of metered holes for gas delivery. But, on the other hand, you have to get it out to clean it and the casting of its rust, because bead blasting would surely plug it up.
I made a back hammer puller for its removal, using a long one-quarter inch ready rod and a slide weight with a wood screw that just threaded into the inside of the end of the discharge tube. By tapping on the end of the rod, the discharge nozzle was removed and not damaged and could now be cleaned as well as the carburetor casting it fits into. The time and effort it takes to remove and replace the throttle shaft bushings has to be done. This old throttle shaft (as with most) was badly worn at the bushing area. The brass bushings were visibly worn to an egg shape. This allows extra air to be drawn into the carburetor past the throttle shaft (especially at idle) and affects the idle mixture quality, and in some cases, even the acceleration of the engine.
After the casting has been cleaned and washed at the bushing area, the bushings are easily removed with the proper sized driver. They are then reinstalled the same way and set at the same depth in the casting as the old ones were. Next, a reamer must be run through the new bushing to remove any brass burrs caused by installation, to align the bushing bores and also to resize it back to the shaft size since the press fit in the casting tends to shrink the bushing bore size slightly. Fit the new throttle shaft into the newly reamed bushings and make sure it turns freely in all directions. Any sticky areas of turning would mean you still need to do a wire brushing of the new shaft or a trip back through the bushings with the reamer.
Final cleaning of the carburetor after bead blasting would consist of the following—first, put on those safety goggles and blow the carburetor out thoroughly with compressed air. Next, get yourself two or three cans of spray can carburetor cleaner with a nozzle tube and start flushing every hole and every port and pocket, first in one direction and then the other. Follow this with more compressed air flushing, then more carburetor cleaner flushing. This procedure should go on until you are SURE every passage is clean of everything, including cleaning beads that may be caught up inside from bead blasting. Then, using a small diameter wire (for example, from a wire feed welder), poke the wire in all of the idle circuit passages as far as you can get it and from both directions; do this several times with all passages. Then again, flush out everything with the carburetor cleaner and compressed air. Don’t be stingy here; one can of cleaner never gets me through a carburetor repair job. With this particular carburetor, I used three cans, but absolute cleanliness here is essential.
I’ll share with you a little one of old Doc’s assembly secrets here that will improve the idle characteristics in the end. When installing the throttle door to the new throttle shaft, it should be noted that the door edges are tapered; be sure to face the taper correctly in the throttle bore and it will be noted that the door will be centered in the bore before the screws are tightened. I like to adjust the door ever so slightly to allow a somewhat larger air gap by the idle gas discharge holes before tightening the screws. This allows more of a Venturi effect past the idle ports and pulls more gas through them and thus a better chance of setting a good idle mixture amount.
When installing any of the throttle door or choke door screws, I recommend a small amount of red Loctite on the threads at final tightening; you don’t want your tractor to swallow any screws. When reinstalling all the brass plugs and the economizer plug, I suggest that a very light coating of liquid pipe seal be used. The secret here is just enough for the threads to seal…NO EXCESS. I also use a very limited amount on the threads of the gas seat and in this case on the seat gasket itself. In this carburetor’s case and with many like it, age and rust have pitted the sealing surfaces where the sealing gaskets land and a little help from a sealant goes a long way in avoiding leaks after the carburetor is put back into service.
There you have it—with a proper float setting and both adjusting needles set at two turns off the bottom of their seats, the carburetor is ready to be given a coating of my secret casting finish. I do not like to paint carburetors, but would rather see them in a bright shiny cast finish and the sealer that I use far outlasts the beauty of any painted finish. Finally, I always hook the carburetor up to a homemade test stand and let it fill up and stand with new filtered gas in it for a while. This assures me that the needle and seat are working and that the bowl gasket on the bottom does not leak. I always install a new bowl drain valve and new brass plugs where needed. If no leaks are present, the carburetor can be drained and installed on the tractor. By the way, the two carburetor installation gaskets are identical except one is always thicker. The thicker gasket always goes to the manifold to keep the carburetor cooler and also helps to prevent the gas from “percolating.”
That’s about it; we’ve just thoroughly gone through a DLTX 63 carburetor for a “D” JD tractor in the “Tractor Doctor style.” This type of rebuild always takes me at least eight or 10 hours to do in this manner, and if you add in the cost of the parts, you’re looking at spending $200 or more. But that seems to be what my customers want and in the end, it’s also the way they like their old tractors to run.
Until we meet again; happy trails—putt, putt, putt.
This column is written by