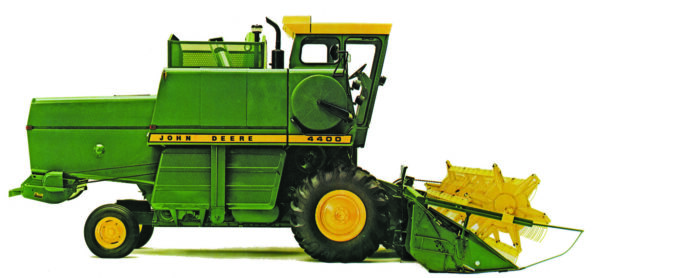
Deere’s first self-propelled combine, the model 55, had paved the company’s way in the harvesting market from the end of World War II through the 1960s. The model 55 was a state-of-the-art combine in all respects and was loaded with features that made it a very strong seller. It was also among the first self-propelled combines to break into rice harvesting and sidehill production. A variable-speed ground drive, large capacity separator, impressive reliability, improved balance compared to other combines and general ease of use all made the 55 a combine that made its owner the envy of the region.
From the groundwork laid by the model 55, Deere created a series of combines, from the mighty 105 to the entry-level 40. The 40 was engineered to sell to farmers who were just switching from a pull-type combine to a self-propelled one and who simply did not have the acreage to justify the purchase of one of the larger machines. Through this market, the 45 brought Deere more combine sales than any other machine. The market began to change, though, and in 1964, the 90 horsepower model 95 became the sales leader, as farms were increasing in size.
Despite its quality, by the late 1960s, Deere’s combine lineup was beginning to show its age. The 55 had been in production for more than 20 years. Even as six different series of tractors passed through Deere’s factories, the 55 lugged on. Dozens of modifications and improvements to the 55 had been made throughout its production life and late 55 combines bore only a passing resemblance to early ones, but Deere had new ideas to improve its combine and bring its harvester line into the 1970s with a surge. It was decided that the time had come to introduce a new line of John Deere combines.
With the brunt of the engineering required for the New Generation’s 20 series finished in the mid-1960s, Deere had the manpower to work on creating a new series of combines. Just a decade or so before, a cab on a combine was seen by many farmers as a luxury for the soft, but operator comfort was quickly becoming much more important to Deere’s customer base and the company was selling more cabs than ever before. Deere made sure to keep this in mind during the production of its new combines. Naturally, farmers preferred the opportunity to get their work finished just as quickly as was possible, so making an increase in power and capacity were also important.
Deere released its New Generation combines for the 1970 model year. The new lineup included the 3300, 4400, 6600 and 7700 combines. The 4400 was Deere’s direct replacement for the best-selling 95, and as such, matched many of the earlier machine’s specifications.
The combine’s new design moved the engine from behind to in front of the grain tank, sitting next to the operator. When Deere was testing ideas for the 55, it found that an engine in this position made engine heat and noise a major barrier to operator comfort. Putting the engine behind the grain tank also created a more balanced machine and put the operator right in the center of the combine. The downside, however, was the fact that the grain tank’s capacity had to be reduced somewhat to leave room for the engine.
Deere’s engineers managed to overcome these problems on the 4400. The first thing that made this possible was the fact that the majority of the machines were expected to be equipped with a cab, making engine noise and heat a much smaller problem. Deere also came up with a couple of tricks to keep the engine clean and pull yet more of the heat away from the operator. First, the engine was completely enclosed. The front of the engine—which could be accessed from a platform next to the operator’s—was covered with a perforated steel door and screens. Deere mounted a fan on the right side of the combine. This fan performed “reverse air flow,” pulling the warm air away from the engine rather than blowing cool air on it. This air was discharged through another screen on the right side of the combine and away from the operator. The covering for the engine simultaneously reduced the volume of the sound coming from it and kept it free from chaff and debris, reducing the chance of debris getting into the engine and causing problems or catching fire.
With the engine next to the operator, there was more room for the clean grain tank, allowing for a total of 72 bushels. The operator, however, was moved off to the left of center on the combine. This was not really a problem, though; just ask anyone who has ever driven a left-hand drive vehicle. Deere chose to power the 4400 with a 292 cubic inch six-cylinder gas engine. This unit was built by Chevrolet for use in its pickups and trucks and managed to produce 92 horsepower at 2,500 RPM. Despite the fact that the 95 had been offered with a diesel engine, Deere did not provide a diesel for the 4400 at its release.
The 4400 came with a variable-speed ground drive, allowing the operator to slow down when coming to a wet, rough, or particularly dense spot in his field. This was attached to a four-speed transmission, allowing the combine to run from about 2 to 15 miles per hour. Drive wheels on the 4400 were 16.9×26 inches and the rear wheels were 7.50×16. The operator was sure to be comfortable in an adjustable seat and the steering pedestal could also be tipped forward or backward as needed. Standard power steering and hydraulic disk brakes also made the ride a fairly nice one.
At the front of the 4400 was the new Quik-Tatch mounting. Deere advertised this unit as making it possible to “combine corn in the morning and switch to beans in the afternoon.” Gone were the days when wrenches and hours were required to switch platforms. Now, the operator just needed to lower the head, disconnect the drive and remove two bolts. The main drive was also easy to change, as it featured a Quik-Coupler which required no tools and, ideally, just a few seconds to connect or disconnect. Attaching a platform was just as easy as removing one and it was said that the whole process from one head to another took only as long as it took to refuel.
Deere released a brand new lineup of corn heads with the introduction of the 4400. Besides being equipped with the Quik-Tatch mounting, these heads had the lowest profile of any on the market, making it easier to pick up downed crops. Deere also revised the drive, enclosing it, making it entirely gear-driven and running it in oil, making regular lubrication of the corn head a thing of the past. The 4400 could drive the regular model 244 two-row, 344 three-row or 444 four-row heads or the narrow row 343 or 443 heads. Grain platforms were revised, as well, featuring Quik-Tatch and revised and accelerated knife sections, allowing for greater cutting capacity. The 4400 could run any of Deere’s 10, 13, 14, 15, 16, 18 or 20 foot platforms depending upon field conditions and crop density.
The feederhouse was revised, producing a crop path that was closer to horizontal. This made feeding easier and reduced the angle that the crop went through when it reached the cylinder. Deere made this a selling point, as well, claiming that this improvement meant “less breakup at the cylinder…less trash to interfere with saving the crop” and that it required less power to run. The feederhouse also featured large access doors on top for cleaning and service.
The 4400’s concave was improved and built with 13 bars and a two-bar extension and the 38 inch cylinder was built heavier and with stronger bearings. The weight helped to act as a flywheel to keep the separator running at a constant speed through thick and thin and the bearings improved durability. A crank on the operator’s platform adjusted the spacing between the cylinder and concave. The rotary deflector, or beater, was run at a speed synchronized to the cylinder. Previously, the rotary deflector ran at a constant speed, no matter the speed setting of the cylinder. Deere felt that this often wasted the front end of the straw walkers, so they set the rotary deflector to adjust the speed with the cylinder—which was also adjusted from the operator’s platform.
Deere extended the straw walkers, revised their shape and increased the throw of the walker cranks, as well, improving grain separation. The 4400 had four walkers, each 120 inches long and with five steps. Grain dropped through the walkers or the concave fell into a new “auger-conveyor” system. Four augers brought all of the grain to the cleaning shoe in the 4400. This system was billed as a Deere exclusive and was an improvement over a traditional conveyor system because grain could not shift to one side of the combine or the other in sidehill operation. Grain also would not overload the system when driving uphill, because augers could move grain in any direction, whereas a conveyor becomes less effective as its vertical slope is increased.
The chaffer and sieve in the 4400 now moved in opposite directions, preventing any plugging in the cleaning area. The adjustable fan was revised as well to deliver a stronger blast of air to help blow out the chaff. The 4400 featured 3,357 square inches of total cleaning area.
With all of these improvements and new features, it is easy to see why Deere felt justified in introducing an all-new series of combines. Many of these features were new not only to Deere, but to the combine industry as a whole. The new 4400 was not just a replacement for the 95. All of the improvements made to the machine made it more efficient and allowed the operator to get more harvesting done in a day with the same size of combine than he ever could before.
Several options were available to make your combine even more suited to your needs. A cab with carpeting, fans, tinted glass, dome light and a rear view mirror was likely one of the most popular. The time when combining out in the hot, the cold or the milo dust proved that you were a man was fading and few 4400 combines without cabs are around today. An adjustable rear axle allowed row crop farmers to put the rear tires between the rows, providing a smoother ride. An optional spring-assisted platform float control helped a farmer to combine low or downed crops without having to worry about digging the head into the ground. A chopper for the back end helped to break up stalks and trash to allow them to be more quickly incorporated into the soil where they could break down and a straw spreader made sure that the trash didn’t heap up behind the combine. Deere also offered a toolbox so that your Vise-Grip had a better place to live than under your feet in the cab.
Deere also listed several other options for early 4400 combines in its sales brochures and on its price sheets. Among these was hydraulic reel lift, which allowed the operator to change the distance between the platform and the reel from the cab. Hydrostatic reel speed control let you match the speed of the reel to your ground speed. An electromagnetic platform clutch made it easy to shut down the platform when the separator was running near capacity, allowing it to clear out before more of the crop was sent through. Each of these were options already available on earlier combines and none of the people contacted about this had ever seen a 4400 without any of these options. However, experience has taught us here at Green Magazine to never say never. If you have a combine without one of these, we would like to hear about it.
Options were also available for the platforms themselves, including a pickup reel for 10 or 16 foot platforms. Three sizes of three-roller belt pickups were also available on the platform to pick up crops previously cut into a windrow.
Improvements were made to the 4400 in 1974. The most obvious change to the combine was to the engine cooling system. Now, instead of the screened in compartment that used to surround the engine, the engine was enclosed behind a steel door. The fan cooling the engine was turned around to blow cool air onto the radiator instead of pulling the warm air off the engine. To keep chaff and dust out of the engine, a rotating screen surrounded the fan. An arm vacuumed the screen once every rotation, removing debris that had been pulled up against the screen and sending it back to the ground.
Very late in the production of the 4400, Deere began equipping the machine with another type of fan screen like that later seen on the 4420. These screens functioned in basically the same way but were inset in a cowling, making them appear a bit different. The heat left the engine through vents at the front and bottom of the engine compartment. Apparently, Deere was now less concerned about the potential for the heat from the engine bothering the operator. All of the cabs sold probably helped to make this decision.
The engine inside that compartment was now a six-cylinder, 329 cubic inch diesel that provided 95 horsepower. This made the machine significantly more efficient and increased its torque compared to the old gasoline engine. Spring-assist for the unloading auger and the toolbox became standard equipment. The posh wall-to-wall carpeting was removed from the optional cabs in favor of a textured rubber mat.
More lights and a rearview mirror were added to the combine’s list of options, improving safety and visibility. Turn signals were also added as an option. Optional grain tank extensions increased the capacity of the tank to 102 bushels. Low-shaft-speed indicator lights could be added. These lit up if the straw walkers, auger-conveyor system, tailings elevator, clean-grain elevator or straw chopper slowed to 70 percent or less of normal operating speed, telling you where the problem was…hopefully before it led to a bigger one. The purchaser could also order heavy-duty final drives on their 4400 and would have to if they wanted the big 23.1-26 inch tires.
The 4400 was also capable of handling Deere’s new 454 four-row row crop head. Those of you who were around when these were introduced know that they were one of the greatest innovations in harvesting since the self-propelled combine itself. Rubber gathering belts brought crops to a rotating tungsten-carbide six-bladed knife, meaning the end of cutterbars. This head was also particularly good at picking up low crops, as it could be run along the ground where it could lift lodged crops into the head and save the grain.
A couple of years later, Deere again improved the 4400. New standard equipment included “daylight-after-dark” lighting, which included four headlamps, three header lamps, one light for the grain tank and one illuminating the unloading auger. Several new options were released at this time, as well. A new “Personal-Posture” seat was optional and could be adjusted five different ways. An electrohydraulic header height control could be added. When switched on, this mechanism kept the row crop head or flexible cutterbar platform gliding along the ground without operator attention. An optional straw walker warning system composed of a sensor on the top deck over the straw walkers. When material built up and tripped the switch, a horn would sound to warn the operator of a possible overload. The optional straw chopper was revised, providing more cutting action and a wider material spread.
Evidence suggests that Deere may have added an optional electric control for the platform float control on very late 4400 combines. This system would have been much like the Dial-A-Matic on a 4420. Again, we would like to know if there were any combines equipped in such a way.
Several new headers were available now, too. These included the rigid-bar 200 series platforms, the aforementioned new flexible-bar platforms and the 453 and 653 row crop heads, the latter of which allowed the 4400 to harvest six narrow rows.
Deere continued to build the 4400 until 1979, when the new 4420 in the Titan series of combines replaced them. 4400s are still popular today on small farms and in special situations where small amounts of a crop need to be harvested, such as in test fields. Just as the 55 and 95 before them, the 4400 continues to be reliable and still impresses with its economy and ability to clean grain, even in today’s fields, where the yield per acre is higher than ever.