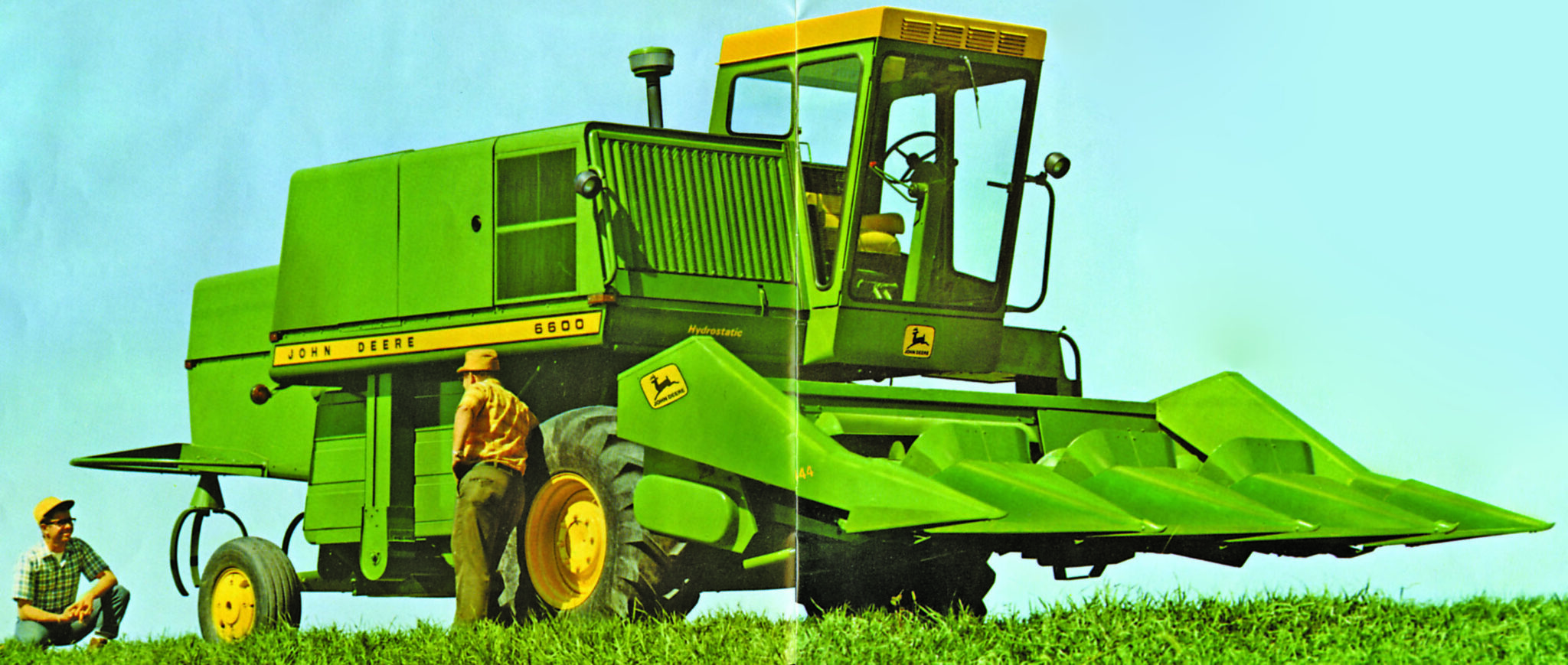
The 105 combine was the monster of its day, reserved for the largest farms, but as farms became larger and yields increased, more and more farmers turned to its large capacity for their harvests. Deereās New Generation combines reflected that and the release of the 7700 brought 25 percent more capacity than Deere offered before. While the 105 was Deereās biggest machine and only farmers of the largest acreages were interested in this big of a machine, the trend for the demand for power by farmers was ever upward and the successor of the 105, the 6600, quickly became Deereās biggest seller of the New Generation of combines.
The John Deere 105 combine had been built to be the worldās largest combine, surpassing IHCās 181ās 46-3/8 inch cylinder with a cylinder 50 inches wide. Deere powered the 105 with a 248 cubic inch Dubuque-built gasoline engine and supplied platforms of up to 22 feet wide to harvest with the machine. The 105 was updated and improved over its lifetime and was later powered by the venerable engine from the 4020, a 404 diesel and 341 gasoline engine. Power, response, and economy all improved, and owners of later 105 combines were happy, indeed.
When the New Generation combines were introduced in the fall of 1969, many farmers who were considering a new combine had little interest in maintaining their same power level. They wanted an upgrade to bring more capacity and efficiency, not to stick with what they already had. As such, the 6600 became the hot seller of the group.
The 6600 was introduced with a Dubuque-built 303 gasoline or 329 diesel engine. These engines provided 104 horsepower, more or less matching that of the 105. The 6600 had a 44 inch separator, 6,486 square inches of separating area and 4,478 square inches of cleaning area. These dimensions were quite a bit smaller than those of the 105 and Deere recognized that buyers might think that this meant that the 6600 was not up to the work that the 105 could do, but they had a response for those farmers. In fact, Deere officials said that the 6600 could outperform the 105. Their reasons for believing this were the many improvements made in the threshing system of the combine. As proof to back up this claim, Deere said that it tested the 105 and 6600 in a barley field in California, each with a 16-foot cutting platform. In that test, the 6600 harvested 2.7 percent more crop. It does not say whether unloading time was considered in the test. The 6600ās larger grain tank could well have given it an advantage. Deere also did not give results in other crops. The point is that Deere knew that the 6600 would be compared to the 105 and knew that the numbers did not immediately favor the 6600, but wanted to be sure that the new machine is seen in a good light.
The improved separation system started with improved feed to the cylinder. Deereās engineers moved some parts around in these combines and created a shallower angle in the feeder house and eliminated the change in angle that material had to make before it reached the cylinder in older combines. These changes made it so that the crop flowed through the feeder house more smoothly and efficiently and made it less likely that the crop would plug through this area.
The concave was extended to 13 bars with a two-bar extension. This longer concave meant that the cylinder was more surrounded by the concave. In other words, a cylinder of a certain size with this new concave would have more threshing area than a cylinder of the same size with an older, smaller concave. This was how Deere was able to justify a smaller cylinder width in its combines. Also improving threshing capacity was the fact that the cylinder was built heavier. This made the cylinder act as a flywheel to keep the separator spinning at a constant speed no matter the amount of material going through it. Adjusting the spacing between the cylinder and concave required just moving a crank at the operatorās station.
The straw walkers in the combines were lengthened to provide more room for separation. The sides of the walkers were straight, which Deere said improved straw movement through the combine, and steps were built into the walkers. The steps allowed the crop to drop down a few inches, changing their movement as they went through the walkers so that the crop would separate from the straw. Deere also lengthened the throw of the walker from four to six inches to āgive your crop a rougher ride to shake out every possible kernel,ā according to Deereās advertising literature. The 6600 had four 130 inch walkers.
Replacing the conveyor chains under the concave and straw walkers was a new system of auger-conveyors. A common problem with the conveyor chain system was that grain would flow to one side of the combine when it worked on a sidehill, overloading the cleaning shoe on that side and possibly spilling grain out of the back of the combine and on the ground. At the same time, working up or down a hill made the conveyor less effective, possibly overloading the chains themselves until the combine was leveled out, at which point a great mass of grain would be sent to the shoe. Five auger-conveyors were installed in the 6600. Each of these took up a section of the combine and was walled off from the next so that grain would not flow from side to side, but always be evenly dispersed from port to starboard. This created a nice even flow of grain to the shoe, allowing it to work properly. These augers also would work at any incline. The grain would be conveyed even if the combine was standing on its nose (do not try this at home). Again, the flow was even no matter the pitch or roll of the combine. One farmer interviewed by The Furrow in 1970 reported that he had switched from a picker-sheller to one of these new combines after looking at the auger-conveyor system. He was quite pleased with the new system, saying, āI know this auger system saved me grain. We had a foot of snow and if there was a kernel on the ground, you would have seen it. You couldnāt keep a bird alive out there.ā
The chaffer and sieve were now built to move in opposite directions, making it almost impossible for trash to get stuck in between the two. The shaking in the shoe was made more vigorous in an attempt to really coax the grain out of the chaff and the fan was improved to deliver more air through the chaffer. The result was better separation and cleaner grain.
All of that clean grain was sent up to a 112 bushel grain tank. This tank was almost 50 percent larger than the tank in the 105. This of course meant you had to make fewer stops to unload, cutting down on the time when you werenāt out in the field harvesting. Unloading came through a 12 inch diameter auger and could be done in 94 seconds.
Given all of those improvements, then, it is easy to see why Deere felt that the 6600 was the 105ās equal in terms of capacity. While the true answer as to whether or not that is the case probably will be lost amongst arguments of speculation and pride, Deere was more than happy to sell the 6600 on that premise.
Deere had more than that to sell the 6600 on, though. The new features of the New Generation combines also included several to make them easier to use and more comfortable for the operator. The engine on the 6600 was moved to the front and positioned beside the operator. This allowed for easier access for service and repair and made possible the larger grain tank. The possible problems with this configuration included the amount of noise and heat that the operator would have to suffer through when sitting right next to the engine. Deere considered this and enclosed the engine in a steel box. This had the obvious benefit of keeping the engine out of the elements, but it also helped to at least somewhat muffle the noise from the engine. Deere also added sound deadening materials in the compartment that enclosed the engine and added a big muffler. Deere said that these things made āthe powerful engines sound like purring pussycats.ā Heat was drawn away from the operator by a fan that pulled air through grates on the front of the engine and blew the hot air out the right side.
Other features to make controlling the 6600 a more enjoyable experience included an adjustable seat and steering pedestal and the ability to change almost any setting of the separator from the seat and without tools. Running a 6600 was certainly easier and more comfortable than running an older combine.
The final improvement to make the operatorās life easier was Quik-Tatch mounting. The Quik-Tatch system was said to allow an operator to change combine platforms in the amount of time that it takes to refuel. You simply drove into a platform with the feeder house down, lifted it up to position the platform, then put in two bolts and connected the drive and hydraulic lines. Disconnecting was done in the opposite order, but was just as easy.
The options list for the 6600 was ample. The most popular item on the list was certainly the cab. The cab was carpeted and had two fans, tinted glass, a dome light and more amenities. While Deere brochures from 1969 showed a number of combines with no cabs, very few of these are around today. Moving up from your old 95 or 105 to a 6600 was a big step. I suppose a lot of the farmers that made that step figured that they might as well be comfortable.
Hydrostatic drive, adjustable rear axle, trash spreaders, hydrostatic reel-speed and hydraulic reel-lift controls, electric platform clutch, a hydraulically swung auger, a perforated auger, platform float control, a stalk chopper and a tool box were also available on the 6600. Many of these options were equipped on nearly every 6600 ever built and a 6600 without an electric platform clutch, for instance, would probably be very hard to find. That said, Iām not sure why you would want to find one.
Deere built a rice harvesting version of the 6600, as well. This machine had the same dimensions and specifications as a regular 6600, but came with tires more suited for slogging through muddy rice fields.
Deere also offered a pull-type version of the 6600. This machine was labeled the 6601. For the most part, the 6601 matched the 6600, but with a 100 bushel grain tank. The machine came regularly equipped with a 13-foot pickup platform, but other pickup platforms and cutting equipment were also available. A Deere 4020 or larger tractor with a 1000-RPM PTO could power the machine.
The farmers of the Pacific Northwest and other regions where farming on steep hillsides was common had to wait for their new combine. This was a special class of farmers and Deere put their needs aside for a time while focusing on those of the flatlanders. The 95 H hillside combine continued in production into 1971, when the 6602 hillside combine finally replaced it. The 6602 sported either a 362 gasoline or a 404 cubic inch diesel engine; each was able to produce 121 horsepower. This additional horsepower was needed in the machine because it had to run an extra pair of hydraulic cylinders. These cylinders leveled the combine as it traveled down the field and were controlled by an air-dampened pendulum system. The air-dampening ensured that the machine did not try to level itself over every bump and jostle through the field. When a legitimate side-slope was driven, the machine would level itself to guarantee that the grain in the separator remained evenly dispersed. The machine could oscillate by up to 45 percent in either direction. The 6602 also had a leveler override switch at the operatorās station. This allowed the operator to change the angle of the machine as he pleased. This was most helpful when unloading into trucks. The auger side could be lifted to clear the side of the truck or lowered to dump nearer the box. The 6602 was driven via a driveline that telescoped from the transmission to the final drives.
The 1974 model year brought a change to the 6600. The engine cooling system was changed. Instead of the āreverse flowā fan sucking air out to the side of the combine, a regular fan was installed on the side of the engine bay. While nearly every combine by this point was equipped with a cab, likely making operator overheating less of a problem, Deere still did not want to blow the hot air from the engine through the engine compartment and at the cab. Instead, the air was directed down toward the feeder house. Of course, having a large fan on the side of the combine just behind the platform was just asking for problems. The fan was sure to suck chaff onto the screen surrounding it and quickly become blocked up and useless. Deere kept this from becoming an issue by adding a vacuuming arm to the fan screen. This screen rotated and the arm sucked trash from the screen and dropped it back to the ground.
The engine inside of the updated compartment was now limited to the 329 diesel, only. The gasoline engine was neither as efficient nor as popular and Deere felt that offering it any longer was unnecessary.
Another new introduction for the 6600 was the unveiling of the SideHill 6600 in 1975. A pair of Deere engineers had noticed rows of shelled corn left behind in a recently combined field in Illinois. They quickly realized that the combine had left the corn there as it traveled down the field at a slight angle. The auger-conveyor system was meant to fix this problem, but it could only do so much. Had the farmer used a 6602, the problem would surely have been remedied. The problem, of course, was that a 6602 was often not worth the added expense for farmers who only had a few shallow hills to worry about. The engineers realized that the hills encountered by farmers in the midwest were probably less than half of the slope of those in the northwest, so a combine built for them need not be capable of as much oscillation. Deereās engineers were able to come up with a simpler, less costly leveling system for a combine.
The new SideHill 6600 could level itself on slopes of up to 18 percent, which was enough for most farms in the Midwest. The same air-dampened pendulum system was used, but obviously, the cylinders and other linkages did not have to be nearly as complicated. Furthermore, the 6600 SideHill used a simpler chain drive rather than the telescoping drive of the 6602. Farmers found that the SideHill 6600 did not only save grain, it also allowed farmers to travel faster through the field, as the self-leveling made driving on the side of a hill safer, so the additional cost of the machine could quickly be amortized.
In 1977, Deere brought another option for the 6600: hydrostatic power rear-wheel drive. This addition made it possible to get into the field a bit sooner after a rain. Rice farmers were especially grateful for this addition. Deere also brought more power to the 6600 and SideHill 6600 combines, putting the 404 diesel in the machines.
Production of the 6600 continued into 1978, but was halted by the end of the year. That fall brought the introduction of the Titan series of combines. The 6600 had spent nearly a decade as the new machine that was bringing in the crops to feed the world.
While the debate is liable to drag on as to whether the 6600 could really live up to the capacity of the 105, there can be no question as to whether or not the 6600 moved the world of mechanized harvesting forward. With so many new features, few farmers wanted to look back to the old days of farming with a 105. Evidence of this abounds, as you are much more likely to find a New Generation combine working in the field today than any of the earlier series.