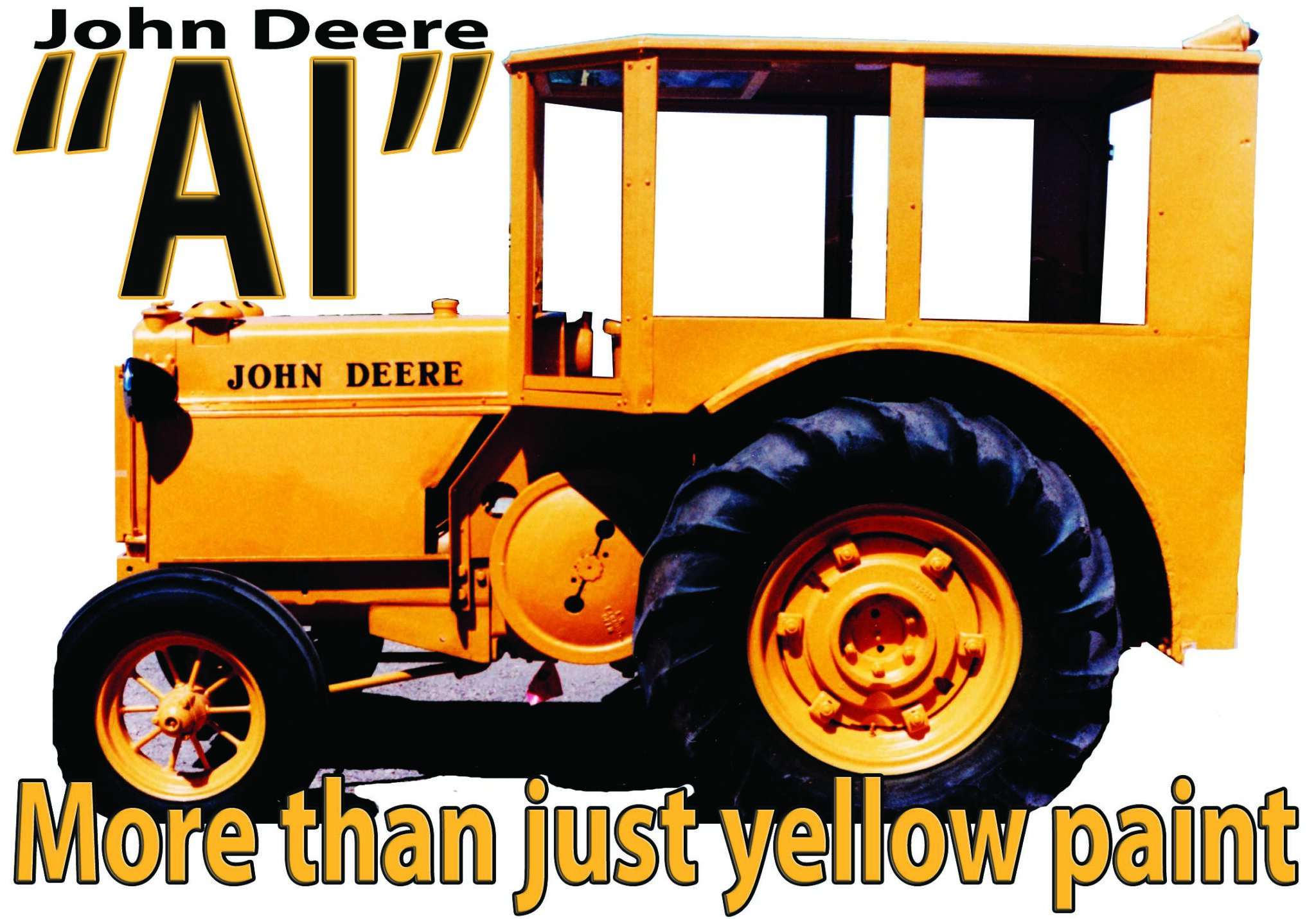
What does a brutally harsh work environment, low initial production numbers and operators who use and abuse their equipment all day long add up to?
A tractor that is highly sought after by collectors and a valuable piece of Deere and Company history.
The John Deere “AI” is definitely a tractor that fits the above criteria to a “T.” Officially introduced to the public in 1936, the “AI” was designed to fit the need of a market segment that Deere felt it wasn’t paying that much attention to and wished to capitalize on the situation. Although some may like to believe that the “AI” is simply an “A” with a funny shade of yellow paint slapped on, there is a little more to the story than that. Deere had projected that around 300 industrial style model “A” tractors would be sold during the first year of production in 1936. So, based on this fairly low projected volume, it is obvious that Deere didn’t want to expend a significant amount of capital to create a radically different chassis for the industrial version of the model “A.” Instead, the company elected to take the “AR” and add a little engineering forethought into reconfiguring it to survive the rigors involved with day to day tasks in the industrial world.
Now, before we begin delving into the details of this tractor, let’s pause for a moment and take a look at the operating environment that the “AI” would have been subjected to. Most of us with a very strong agricultural background typically tend to treat our equipment, particularly tractors, with a pretty high level of respect. This mentality has been ingrained because for many, many decades, the owner of the tractor was also the operator and tractors have typically been the center point upon which agricultural operations revolved. The tractor was a very large investment and if it broke down at inopportune times, planting couldn’t occur, harvesting ground to a halt, cultivation was brought to a standstill and the list goes on and on. So, it was in the farmer’s best interest to take care of his tractor to ensure costly breakdowns didn’t occur or at least happened infrequently.
However, on the other side of the coin, in the industrial world, the operator typically doesn’t own the tractor, so they usually did not have a vested interest in whether the tractor was operable or not. Perhaps needless to say, the operator abuse level that had to be endured by the tractors destined for the industrial market was very high. So the little things, like checking and changing the engine oil on a regular basis, making simple adjustments and lubricating critical components, sometimes did not get performed as it should have. Also factor in that the pure nature of the work was brutal as well. Building roads, digging ditches and plowing snow (to name a few examples) are typically performed in terrain that can quickly render an ordinary tractor inoperable if the right precautions are not followed. Granted, not all industrial settings can tax a tractor in the environments listed above since some industrial tractors reside in factories or warehouses where they simply pull loads from point A to point B on smooth, level surfaces. But often times, these tractors suffer from “crank and go” operation, where zero attention is given to the tractor as long as it runs and does the job. When we consider these criteria in which an industrial tractor will reside, there is a little more than painting a tractor yellow and putting an “I” suffix to the model designation and Deere engineers realized this and took the appropriate measures to at least give the “AI” a fighting chance in the industrial world.
One may ask why the “AI” was chosen to be a derivative of the “AR” and not a descendant of the General Purpose model “A” chassis. After all, the production numbers were remarkably higher on the row crop model “A” and economies of scale would have dictated that with a higher volume of common parts, the “AI” based on a row crop chassis would have been far less expensive to manufacture. But you only have to consider one fact, which is that the row crop chassis of the model “A” has a center of gravity that is relatively high off the ground, and even when equipped with a wide front end, the chassis can be unstable when operating in extreme terrain conditions.
The “AR,” on the other hand, has a very low profile, resulting in a center of gravity closer to the ground and a much more stable operating platform. Couple this lower center of gravity with the low profile and you have a tractor that is much less apt to tip over and can get into those tight spots without having to duck your head or worry about ripping off a muffler or air intake pipe. So, rallying around the “AR” was about the only logical route Deere could take to bring the “AI” to market in a timely fashion without incurring the tremendous costs associated with a new chassis design. Thus, there are a number of similarities with regards to the “AI” and the “AR.” Large items such as the engine and the transmission for the most part remained common with the “AR.” Therefore, we’ll focus specially on the changes that made the “AI” unique from its close cousin, the “AR.”
One of the biggest identifying features on the “AI” that makes it stand out from the crowd is its front axle. The engineers recognized that being able to finagle these tractors into and out of close quarters would be a very desirable trait to have in an industrial tractor. To help address this, they relocated the front axle approximately seven inches towards the rear of the tractor. This allowed for a very tight turning radius, with the “AI” now having a wheelbase of only 69 inches, allowing the tractor to turn on a dime, so to speak. Another added benefit of moving the axle towards the back was that integral equipment could now be mounted to the front of the machine and the engineers no longer had to worry about hitting the tires. By providing an area at the front of the machine for auxiliary equipment to be easily mounted, the use of belts to power the auxiliary equipment became very easy. Take the centrifugal water pump manufactured by Sterling Machinery, for example. With the pump mounted at the front of the tractor, providing belt power from the clutch pulley was a simple feat to accomplish. Another notable departure from the “AR” was a little less visible, but nevertheless important. The “AI” utilized larger diameter rear axle bearings to support the rear axle and wheels. The “beefing-up” of the rear axle bearings was a testament that the design engineers were very well aware of the tortures that the “AI” may see during service and decided to give it a little help to ensure it remained on the job. While they were at it, the engineers added flanges to the ends of the axle to make adding optional turning brakes easier.
Along with the change in rear axle bearings, the “AI” received a different style of service brake—the handle that engaged the brake was up on top of the maincase, which allowed for easier access when the brake was to be engaged. This new design increased the leverage on the brake and incorporated a new pivot point that reduced the complexity of the overall design. One other major change that the “AI” experienced as it was converted over from the “AR” was the drawbar. A much stouter drawbar was added to help shoulder some of the burden in towing equipment behind the “AI.” An optional pintle hitch was even offered to make life a little easier for the user of the tractor when it came to hooking and unhooking equipment from the “AI.”
Although the “AI” was a close derivative of the “AR,” the “AI” did share some common parts with the “AO” as well. As mentioned before, a low profile is desirable for an industrial tractor, and with the muffler and air intake pipe sticking straight up in the air (as was the typical design on the “AR”), these parts could have been a hot commodity in dealerships, as the industrial users would have been knocking them off left and right. A decision was made to integrate the lower profile muffler and air cleaner intake stack from the “AO” to help avoid damage to these components during operation.
One final noteworthy change that was made during the creation of the “AI” was the operator’s seat. While the “AR” used the steel seat pan design, which had been around since about the beginning of mechanized agriculture, the “AI” went off in a different direction and incorporated a cushioned seat. This new style cushioned seat was nested inside of a metal frame, which incorporated a “high-rise” backrest. Not only did this new seat take out some of the bumps and bruises to the operator’s posterior side when the tractor was operated in rough terrain, but the integral backrest somewhat cradled the operator and helped to prevent him from falling off the tractor when the going got rough. This new style of seat with the cushioned bottom also allowed engineers to eliminate the spring suspension from the tractor and mount the seat directly to the rear axle housing. Of all the features on the new “AI,” I’ll bet you can’t guess which feature the operators liked best about the “AI”?
In a nutshell, that’s about all the difference there is between the “AR” and the “AI.” As you can see, these two tractors were closely related except for a few key differences. But the story of the “AI” doesn’t stop with just the differences between it and the “AR.” The “AI” had a fairly broad list of options that could be ordered to help tailor the tractor to the job duties that it would perform. Some of the more unique and interesting options included a unique overdrive option for the transmission to increase the travel speed of the “AI” to help get from job to job in a little more expedient manner. The traditional power shaft could be ordered as an option, similar to the “AR,” but the “AI” could also be equipped with a side power shaft assembly to facilitate powering special auxiliary equipment. Other options included a front bumper with extensions if desired as well as a rear exhaust. There was also a wide variety of wheel and tire options so that traction concerns could be addressed as well as the option of electric starting and lighting. All of these options added up to an industrial tractor well suited to handle any task within reason.
While Deere had good intentions for the “AI,” when it came down to actually moving the iron out the door, the expected sales that Deere anticipated simply were not there. This resulted in a total of 91 “AIs” produced between 1936 and 1941, at which time the “AI” designation was dropped from the lineup.
But just because there were fewer than 100 of these tractors ever built, and given the fact that most of us will never have the pleasure of ever owning one, that doesn’t automatically mean we should toss the history of the “AI” into the closet and forget about it. The “AI” marked the early beginnings of Deere’s venture into the industrial market, which would eventually blossom into a very profitable enterprise of Deere and Company. Even if the “AI” wasn’t a sales sensation, we can still enjoy the history of the machine and reflect back at how this machine was intended to be utilized and some of the steps that the engineers took to help make the tractor a success. At the very least, I hope now that when you see an “AI” at a show, or hear a discussion about an “AI,” you can appreciate the fact that it’s much more than just an agricultural tractor painted yellow. And hopefully you can appreciate a little more how the “AI” was utilized back in the late ‘30s and early ‘40s. Although we would like to think that the service life of the “AI” was as glorious as the advertising literature depicted, with the operator smiling away, wearing a pith helmet and mowing the ditches along the highway on a nice sunny day, when the truth be told, the “AI” was down in the trenches (literally) battling away and helping to construct the roads and buildings in an ever-expanding America. When you look at it in that perspective, it is truly amazing that the mortality rate wasn’t higher than it was and that there are still some surviving examples of the “AI” today. That, in and of itself, makes the “AI” a truly noteworthy machine and one valuable piece of Deere’s history.