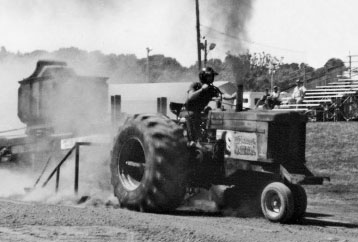
By Bill Grimes
Ever since my experience as a teenager with turbo installations on a couple of two cylinder Deeres—an “A” and an “R”—I had often found myself wondering which of the horizontal two cylinders would be best suited for turbocharging.
I came to the conclusion that the shorter stroke diesels of the 70/720/730 series with their center main bearing would be the best candidates, as not quite as large a volume of exhaust would have to be pushed through the turbo all at once and the potential for operating at higher RPM would be a plus. I had to wait about 15 years to find out if my assumptions were correct.
Around 1995, I was able to purchase a “running” (I use the term loosely) 70 diesel from my friend, Joel Fahnestock in Meyerstown, Pennsylvania. Joel is an expert John Deere mechanic and owns a tractor repair business where he feels right at home working on anything from antiques to modern farm tractors to pullers. Joel offered me the 70 for $750, provided that I give him back certain stock parts that I wouldn’t be using. That sounded like a good deal to me!
Now here was a tractor cheap enough that I wouldn’t mind doing a little experimenting with it. I intended to transform the old 70 into a very low budget puller for the super antique class, and at $75 apiece, used turbos were a lot cheaper than boring and stroking. The expense of a fresh paint job wasn’t even considered, as a shiny hood never got anybody an inch farther down the track. Besides, I’ve always found the weathered, faded look earned from many years of hard work uniquely attractive and more suited to the machine I intended to build. I guess I’m in the minority but I just don’t have any fun at the pulls if it costs a bundle to consistently win that elusive first place trophy. I enjoy the challenge of building a winner out of whatever I can find lying around, making any necessary modifications myself, while spending the least amount of money possible.
After stripping the tractor down to just the rear, main case and engine, it was time to yank off the head and see what we had to work with. The good news was it had already been bored .045 over, albeit many years ago. The bad news was that the left-hand snap ring on the number two piston pin had either come loose or had never been installed properly and a couple thousand hours of operating with the pin rubbing the cylinder wall resulted in two seven-inch long grooves deep enough that even boring .125 over wouldn’t take them out.
The possibility of boring and sleeving that cylinder or perhaps finding another block briefly went through my mind, but I quickly rejected those ideas as they would actually cost money. No, all I needed were two welding rods, a 4-1/2 inch hand-held grinder, a cylinder hone and about two hours, all of which I happened to have close at hand.
It’s a little character flaw of mind; I’ve just never been able to justify spending money on a pulling toy to fix it right when you can get essentially the same results patching it up with a little “blacksmithing,” as my dad would say.
Oh yes, I forgot to mention that the splines on the flywheel end of the crank were shot, too. A few more 7018 welding rods and a little more grinder work and we had our splines just enough oversize to fit the also worn out flywheel.
Lest you think my work is a little on the rough side, I’ll assure you that I make liberal use of dial indicators, micrometers, straight edges, etc. when making such repairs. Both jobs turned out great; the flywheel has never come loose and that cylinder still carries good compression. (If you think these fix-it jobs were too difficult to get right by doing them freehand, I’ll have to tell you sometime about using a five-inch hole saw to cut the cylinders completely out of a John Deere “M” block and fitting 8630 sleeves in.)
I did lower the compression ratio just a little and cut some valve reliefs in the pistons, ported and polished the head, added dual valve springs (springs from a “B” will fit inside the 70’s springs with a little massaging), lightened the pistons by trimming the skirt considerably and the pins by machining the inside a little. (I made many more changes to the rod piston unit a couple of years later.) The addition of 830 pumps and injectors, an extra oil line to the center main and some homemade copper “O” rings to fit in the trimmed head gasket to help hold all the combustion pressure and my engine was ready for the addition of a turbo.
I took what I had learned from my experience with the “A” and “R” and set to work designing the set-up. I did not utilize the stock exhaust or intake manifolds as I wanted to build an exhaust “header” with separate runners from each cylinder feeding the divided exhaust housing. Turbo sizing can be a little tricky; the rule of thumb is usually a turbo from an engine of similar size and RPM range will probably be a good fit, but we have to throw this out the window when John Deere two cylinders are involved. With the large volume and length of the exhaust stroke, the turbo size must be much larger than you would think so as not to cause too much back pressure. Believe it or not, the TV-61 turbo from the 619 cubic inch 8630 is a perfect fit for the 376 cubic inch 70 diesel. As with the “A,” a large holding chamber (about 1-1/2 times the displacement of the engine) was used on the intake side. Along with water injection and a couple of other little tricks to make it work more smoothly, the tractor ran well but honestly has never performed at quite the level I had hoped. With 23.1×30 tires on the rear, I could pull in fourth gear in the 5,000 pound class. The turbo would produce about 40 pounds of boost at 2,500 to 3,000 engine RPM, which was around 18 to 20 miles per hour and it would hold good boost even when lugging down to stock RPM!
The only mechanical breakage to occur thus far has been two tappet adjusting screws. The John Deere clutch is an amazing this—even though it has the same old disks in as when I bought it, the clutch has held up without slipping all this time.
In the late 1990s, the 70, known as Hazardous Material, along with a bored and stroked 720 diesel (also built for very few dollars) that my dad, Oscar Grimes, drove were the tractors to beat in the southern Maryland area. We also enjoyed pulling on Maryland’s eastern shore, in Delaware, and in North Carolina. My cousin, Will Shepherd, still likes to pull the 70 once or twice a year locally and does well even though it’s about worn out now.
I’ll just say, in my experience, turbocharging two cylinders can be done successfully, but it’s a little more complicated and you will not get the level of performance that you get from a four or six cylinder tractor of similar vintage.
What’s next for Hazardous Material? A second turbo? Converting it to two stroke? It is possible. I’ve given considerable thought to each, now if I could just find the time—because I think we both know that I’m not going to spend