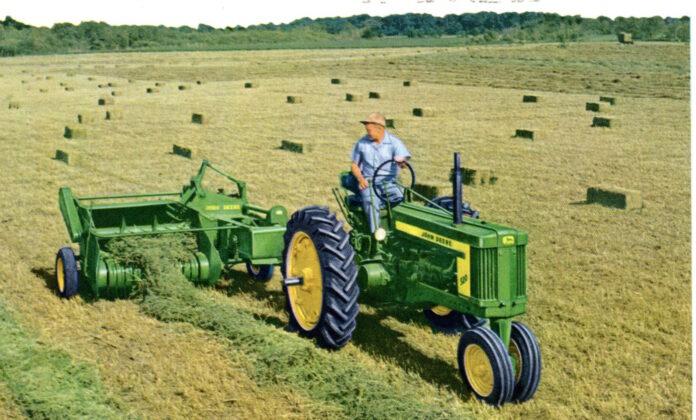
Testing torque
Get out your slide rules because you’re going to learn all about torque and how they used to test it. You’ll also learn about PTO and engine clutches. You probably won’t find too much to argue about in this installment but even if you do, don’t call the editor.
Another thing that has promoted the type of performance you fellows are selling today is John Deere’s acquaintance with good combustion chamber design and it has paid off—all the hours that we have spent having one of the foremost mechanical engineers in the country fuss around with changing the shape of a piston and a cylinder head.
Go back to the automotive trade again—I think Studebaker started talking about the importance of turbulence in the combustion chamber and what part it played in promoting efficiency in an engine. If you go back to about 1950 and look at their old advertising, you will find that they were about the first one and that is when they started talking about it. You fellows started talking about cyclonic fuel intake in 1939, I hope you did, that is when we started talking about it. We knew the importance of this thing—we were working with it—working to bring you the championship performance that you are selling today. When we came out with the present type of piston design and cylinder head that we have, we did so because again we felt that we could squeeze just a little bit more help than was offered by the cyclonic fuel intake, you know with the eyebrow over the intake valve and the swirling motions of the fuels that came into the cylinder creates a turbulence so it can break down the balls of gasoline that come in from the carburetor into smallest possible particles. You do that so you have a better chance of getting them to mix with oxygen, uniting and forming combustion and power. This happens in our modem engine when the piston comes up on a compression stroke. All of the material represented by the flat area on the head of that piston that’s got to squeeze into that concave section in the head and the time of most activity your turbulence is right at the time that we want to touch off that mixture with a spark plug. What could be better? That is the thing that has brought us out as leaders in performance, that coupled with this duplex carburetion and the other features that we have had in the past. It’s no accident—it isn’t luck—it’s hard work and is real value.
It’s a thing, too, gentlemen, and I was going to bring this out a little bit later, but I am going to hit on it lightly right now—that is responsible in part for the lugging ability that we have in John Deere tractors. As long as we are talking about our success at the University of Nebraska in the tractor test program, let’s bring this quality of lugging out. It is another basic product of our two cylinder design. You see in the Nebraska Test now they have a section covering engine torque. I want to tell you a little bit what that means, so that when
you consult these tests, you will know better what happens. The Nebraska tests are good, but I am going to point out a little fallacy of the tests as a means of telling people about your product. The way they run this torque test is this—the manufacturer of the engines states that such and such is rate of speed. Then they hook the tractor into a dynamometer and they decide that they are going to take the torque reading at rate of speed five percent less than rated speed, 10 percent, 15 percent, etc. on down to about 50 percent. They make this decision arbitrarily before they ever start testing the tractor and they figure out what 95 percent of rated speed is in the form of RPM. If it is a 1,000 RPM engine, of course, 95 percent of rate of speed would be 950 RPM. And so on they figure out their percentage down to 50. Then they hook the tractor into a dynamometer with a belt—a dynamometer is nothing more than an electrical generator. When they start the engine up, the fellow stands over here and he turns the rheostat putting a load on that generator until he slows that tractor down to rated speed. Then they take foot pounds torque reading on that tractor—what the twisting effort that machine is actually producing. Now remember he knows what speed that engine is to run at when he takes a 5 percent of rated speed torque reading—he knows this all beforehand.
How did he find out what that tractor will do then at 95 percent of its rated speed? He slowly screws down this rheostat until he has slowed that engine down to that given speed. He has as long as 20 minutes to do that. Slowly let that engine adjust itself until it evens out at this predetermined 95 percent of rated speed. Then they take another torque reading and these are the values that are shown in the NEbraska Tests as for as torque. These are the values of reserve power that are supposed to spell out the lugging ability of an engine to you.
I’ll say right off hand the way they are published, it looks as though your competitors in a lot of conditions do as well as you do. They’ll come up within a range of, say for instance on a diesel engine, of having a 16 percent torque reserve over what they show in rated speed. But the heck of it is, fellows, that’s not the way the load comes on in the field. You see the load in the field comes on right now, not in 20 minutes. You’ve got a plow behind your tractor, you are driving along, you come to a hard spot in the field, maybe a row that you have been running out on or a little lower spot, a wetter spot, a load doesn’t come on in a matter of 20 minutes, it comes on now. Right now your tractor is asked to put out some power, some twisting force to take on this undue now. How is it going to do if it’s built so lightweight that the load is going to take hold of the engine and slow it down so fast that the engine doesn’t have time to adjust itself? It can’t do it even though that engine showed tremendous lugging ability at the Nebraska Test. I’ll tell you what happens. In this two cylinder antiquated design, when you plunge into these various peak loads, there is tremendous weight and inertia that you’ve got built up in these heavy old obsolete parts to fight the tendency of this new load to stop you just the same as the brakes on a Cadillac have to be bigger than a Chevrolet to stop you at a given speed in a given length of travel. This heavy mass and tremendous energy stored up here fight this new load toward slowing it down. It is the inertia that we are taking advantage of. Then it gives the governor time enough to do its job.
You see that when people have been out plowing in the field and have been able to count the power strokes on the John Deere tractor, they have often remarked, “My, what a wonderful governor.”
“Yes, it’s a wonderful governor. It’s a wonder we still use the thing. I’ll tell you why we do. We can build it at the cost that we do and it just has all the durability in the world. There is no sense in changing it, but that isn’t where the wonder is. All this air and fuel in the induction system, for instance, is subject to the same loss of mass and inertia as is the crankshaft. Now when this newly induced load tried to slow down the tractor, if your governor opens up, for instance, on a lightweight machine rapidly because your speed is going down rapidly, it will open the throttle on the carburetor but now where you are not going to make the difference is this, that there is not enough time then left in the manifold to exhilarate your fuel and air mixture and get it down in the cylinder in larger quantities enough to keep your engine going. In this job, the crankshaft inertia maintains the load long enough for you to get a heavier charge of fuel and air into that combustion chamber.
Gentlemen, understanding this will spell out the success or failure of a field demonstration to you. There is one thing that ought to teach you how to go out and successfully demonstrate our line of tractors. I don’t care whether it’s got a whoop-to-do stick on it, a torque substitute as we sometimes call them, or what it is, there is a thing that can make you top dog. You go out and load a John Deere tractor so that about 85 percent of the time left, the tachometer needle is down on the mark that says rate of speed. Maybe 15 percent of the time it is pulled down below the rated speed to the point where the engine just darn near stalls. You so load your tractor with a plow, you plow for a given length of time and then just boldly get off and challenge anybody with a tractor of competitive price and size to get in and duplicate the job you have done and they are not going to do it and I’ll bet my bottom dollar on it. If all you have to know to go out in the field and keep from getting beat, that is quite a lot. That’s where the basic difference lies.
I am going to talk for a few minutes above improvements in our John Deere design. We certainly admit that we are not so perfect that we can’t stand improvement and we improve as has been our practice in the past continually. I think this can be verified by the changes in design of your power takeoff, power steering— changes that we have brought out in the transmission in the clutch.
Look at this power takeoff for a minute. We were having some difficuIty with rather abrupt engagement of the power take-off shaft. This was particularly noticeable on tools such as a mower or on some of the combines that it was necessary to line up a little dog-type clutch to operate an unloading auger on the combine. Of course, the customer made an error in the first place if he had such a combine in his possession. He should have had a John Deere and he would have been all right.
But we smoothed out the operation of this power shaft clutch to where it’s a feather touch proposition. Our clutches don’t have any barrier in its field to greatly reduce the amount of effort needed to engage the clutch over what we knew in the past and also have provided a positive neutral clutch position. That is a neutral position now that you can put the clutch in neutral and go back and take hold of the power shaft and turn it freely. That reminds me of something turning it freely in neutral position.
The Minneapolis Moline people came out with a new tractor they call a Five Star. But I would like to have you notice their power shaft. You start up the tractor and they have some form of clutch on it and if it’s anything like the one we bought in Waterloo and I might add for your information, too, that when we talk competitively about these tractors, we have an idea what they will do because we buy one of each model that is put out on the market. I suppose our competitors do the same thing. I know some of them do because we get requests for tractors from them. But this Five Star job, you engaged the clutch, look at it and it’s turning. You disengage the clutch and it is still turning. You get off to find out whether you have the right lever or not. You are going to take hold of that clutch and stop it when someone moves the lever and you’ve got a job on your hands. It can be done, but you’ve got to have the engine idling just as slow as possible and you’ve got to have an awful strong hand to hold that shaft from turning. That’s why we put a brake on our shaft, gentlemen, so that when the operator gets off the tractor, sticking his fingers in the snapping rolls or some other thing he shouldn’t be doing, that brake will keep that power shaft from turning and accidentally maiming that man. We felt this was important when the previous control was actually a gear shifting device. We didn’t want anyone to go off half-cocked, thinking that by moving that lever they have actually slipped the gear. You know a wet type clutch always has the ability to creep a little, unless you positively prevent it.
Minneapolis Moline hasn’t done this. With that neutral position, you can take into fully engaged over center with as much ease as you desire. Feather touch certainly is a very nice clutch. There are some changes on the transmission that I am going to briefly hit on. I suppose you fellows have read your bulletins about it. If not, I suggest you back through your field service bulletins and take a good look at it. We have had a little difficulty in the past, I saw with a certain degree of reservation, of tractors being difficult to shift or sticking in two gears at once. There was one reason one of these tractors ever got in two gears at once and it is not because somebody just took hold of the neutral gear shift lever and put it in one gear and had it in two. It got in two gears at once by some fellow taking a #12 muddy boot and beating on it because he couldn’t get it out of gear or taking a 2×4 or something else and he left it in one gear and then put it in another.
Now that difficulty arose, gentlemen, because we have not been able to entice Mr. Farmer and in a lot of cases, Mr. Dealer, with getting acquainted with the proper adjustment of the pulley clutch. We have talked about it and apparently it has gone unnoticed. I want to bring your attention to it. You see the big thing is the fellow grabs hold of the lever and pulls back on it. When he pulls back on that lever, he is re-engaging his clutch, but he doesn’t know it. That is the thing that we put this new type of adjustment in to prevent. What happens when he pulls back on this lever? You know that clutch fork pulls the clutch operating sleeve around the pulley and when you pull back far enough on that lever, it pulls that clutch operating sleeve in toward the center of the tractor. When it gets so far in, the back side of that sleeve hits the gear on the end of the pulley and it pulls the whole pulley in toward the center of the tractor.
Now here is the fallacy of it—the crankshaft hasn’t moved and the clutch driving disk that is splined on the crankshaft hasn’t moved, so when you pull the pulley in, you are pulling with the pulley, the pulley bolt and the pulley bolts are pulling on the pressure plate and the pressure plate is pulling that last set of linings up against the clutch driving disk and you are reengaging your clutch.
How does a farmer fix it? He gets out here and he adjusts the pulley brake. Every farmer who has had a John Deere tractor for years knows how to adjust this. He pulls back on the clutch, he’s pulling it in gear and he adjusts the pulley brake and he is trying to stop it at the same time and it doesn’t work and that’s how we get into this transmission complaint. This new device here on the front of the first reduction gear housing is for the purpose of making an adjustment so that it is not possible to pull this clutch fork into the point where you can pull the pulley in until you re-engage the clutch. You can learn how to make that setting from information in the field service bulletin and you will be out of any difficulty as far as transmissions staying in two gears at once and it will certainly make a difference in the ease with which your customer can shift his tractor.