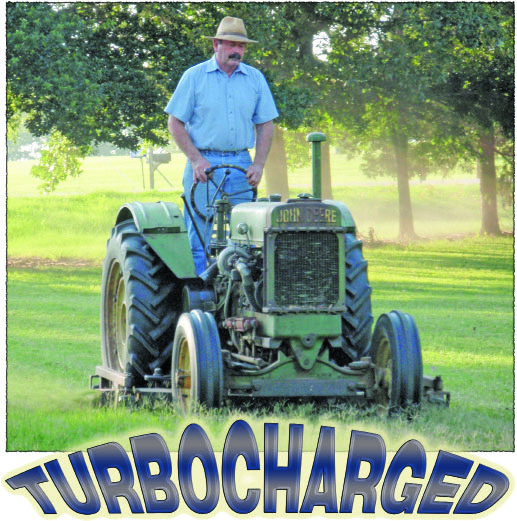
I am writing this in response to Mr. Thinker, who (in the August 2010 issue of Green Magazine) asked for reader input from those who have had any experience with turbocharging two cylinder John Deeres.
I have a 1944 John Deere “BR” on which I have built a 72 inch belly mower. I mow seven acres of lawn with it. I like to mow in third gear. Previously, I had to clutch quite a lot to keep mowing that fast. (I have designed an independent PTO operated from the flywheel of this tractor, but more on that later). That is when I decided to turbocharge the tractor. Also, at that time, most people thought that I should be mentally evaluated (in fact, they have never stopped thinking that!).
Most, if not all, turbocharged tractors are diesel and do not have a carburetor with a butterfly. The turbo is able to get as much air as it wants. The engine speed is governed by the fuel injection pump. This engine is different in that it is a gasoline engine with a carburetor and fly ball governor. I could not turbocharge the engine through the carburetor, as the turbocharged pressure would not allow the carburetor to work properly. So I decided to make it a pull-through system by placing the carburetor on the inlet side of the turbo. As far as the carburetor is concerned, it does not know it is on a turbocharged engine.
I machined an adapter to bolt the turbo from a four cylinder Chevy engine directly to the exhaust manifold of the “BR.” The muffler mounted to the “BR” manifold with four bolts. I then mounted the carburetor on the inlet side of the turbo. I had to re-route the air intake from the oil bath air cleaner as well as the air-fuel mixture from the turbo to the intake manifold. I also had to build new linkage from the governor to the carburetor butterfly. Oil to the turbo was taken from where the oil pressure gauge is installed. I have not noticed any drop in oil pressure.
Operation of the tractor is no different than before turbocharging—except now I do not have to clutch in the tougher spots. It may be a half a smidge harder to crank (hand crank) as the air fuel mixture has to travel farther to the combustion chamber. I usually choke it for one or two more pulls than before and it runs rich for a couple seconds after starting. Other than that, I have not noticed any problems over the last eight years of operation with this turbo. As far as I know, the tractor has never been overhauled.
The interesting thing about this gasoline turbocharged tractor is that under most all conditions, the engine is still running on a vacuum. However, when a full load is applied and the governor opens the butterfly all the way in the carburetor, you will hear the turbo spool up and the vacuum-pressure gauge will move from vacuum through -0- and then will display about one pound of boost on the intake manifold. After getting through the tough spot or if the clutch is pulled and the throttle butterfly is no longer in the full open position, the turbo will spool back down and the engine once again goes back to running on a vacuum.
One may not think that one pound of boost is a lot—but for a 66-year-old engine that is used to running on a vacuum—it is. This tractor was shipped to Brandon, Manitoba, Canada in September 1944.
My first experience with turbocharging non diesel engines was with irrigation engines on the high plains of Texas in the 1970s. I would turbocharge 413 cubic inch Chrysler industrial engines running on natural gas by inverting the exhaust manifolds, y-ing them together and mounting an air research turbo on that, then mounting the natural gas carburetor on the inlet side of the turbo. There were no governors on these engines as they were on a constant load—that is, if the pump shaft did not break or a U-joint go out (always in the middle of the night). It really did not matter, though, if it were in the middle of the night or not—only woke you up from a good sleep when it happened in the middle of the night! In that case, they would just open up and have a cast iron fit and eventually throw themselves over 40 or more acres.
Although this tractor is changed quite a bit from the way Deere built it, not a single hole was drilled in the tractor, nor was any welding or other machine work done to the original tractor. When I am ready, I will completely restore the tractor to original condition, perhaps with the mower deck on it.
I bought this tractor from Don Peck in Zearing, Iowa. The tractor was originally shipped to Brandon, Manitoba, Canada in September 1944. After I got it home and ran it around with nothing to do, I started thinking it would make a great tractor to mow my seven acre yard with as it is not very high and would get under the tree branches really well.
I have a 332 diesel lawn tractor with a 50 inch deck that really works great, but I wanted to get the job done faster as well as be able to drive the “BR.” I measured the “BR” tractor and scaled up the 50 inch deck from the 332, then designed a deck to fit under the “BR.” By using math and measuring the pulleys on the 332, as well as determining the speed of the engine on the 332, I found that the tip speed of the blades on the 332 were traveling 19,000 feet per minute or 216 miles per hour. The engine of the “BR” only turns 1150 RPM. I would have to do some fancy gearing to get the tip speed up to 19,000 feet per minute.
I also wanted the “BR” to have independent PTO as well as hydraulics to lift the mower deck. So I designed both these items into my design. The hydraulics were accomplished by mounting a donor power steering pump off a Chevrolet Vega from a salvage yard. (But don’t tell the “BR” that.) The pump fit on the front fan shaft support without drilling any additional holes in the support. The pump is driven from the generator pulley as this tractor is a hand start and has no lights. I mounted a two spool hydraulic valve under the radiator of the “BR” and made linkage from the steering post down to the valve.
I incorporated the independent PTO into the drive system for the mower deck. In order to get the speed increased to give me the 19,000 feet per minute tip speed, I used a donor rear axle with third member from a rear drive Honda car (again, please don’t let the John Deere tractor that). The right hand axle of the Honda rear end was cut off at the third member and the banjo housing was plated for strength as well as to keep the oil in it. I then welded the spider gears in the third member together. Next, I mounted the rear axle crossways on a pivot under the main case of the “BR” with the third member located to the right of the first reduction gear and inside the right drive tire. Then I proceeded to machine a “B” section sheave for the axle and installed it where the rear wheel used to be mounted.
Next, I took a donor flywheel from another hand start “B” John Deere and machined a “B” section sheave to mount on the outside of this flywheel. A “B” section belt is used between the two sheaves. I had to machine a one-half inch thick spacer to space the left hand drive wheel out for clearance. Since the Honda axle is supported on a pivot, the belt is tensioned by pivoting the axle housing. This is done by using a two inch diameter hydraulic cylinder located behind the flywheel and attached to the Honda axle housing. There you have it! Independent PTO. I shoulda been a Deere engineer. There is absolutely no power being transferred to the mower deck using the original PTO. (I may use the original PTO at a later date to mount a starter on for the “BR” so I can start it in my old age.) Now since the rear axle from the Honda was driven backward and since the spider gears were welded, I had 3,500 RPM coming out of the propeller shaft of the Honda axle facing forward and turning the correct direction.
I used 25 inch John Deere blades for the mower deck so I could just go to my local dealer to get them. They always get confused when I tell them what model mower I have. For the deck spindle bearing supports, I used four bolt trailer wheel hubs that I machined to take ball bearings instead of tapered bearings. I built larger diameter shafts with larger bearings using the design of those on the 332. Power was taken from the Honda third member via a short driveshaft to a 90 degree gearbox on the mower deck. This allows the deck to move up and down without any problems. Two belts then deliver the power to all three blades. The deck is raised using a three inch diameter by four inch stroke hydraulic cylinder. The deck rides on four turf tires when mowing and is fully floating. I also built a wind tunnel into the deck and it really does a nice job mowing. I actually prefer using it over the 332. The neighbors like to hear it run, also. It cuts mowing time down to less than half the time. Every time you make one round, you have cut 12 feet of grass!
Submitted by,
Richard Kuper, BWT
(baling wire technician)
Charleston, Arkansas